Clayton Home Building Group and the University of Tennessee’s Department of Industrial Systems and Engineering are implementing workforce changes developed from more than two years of research.
The research project began in early 2018.
Clayton’s university partnership broadens the corporate and industry commitment to making homes more attainable by incorporating advanced automation and robotics into the off-site construction process that improves efficiencies and reduces cost.
“Our country is experiencing a widespread need for quality, affordable housing solutions,” President of Clayton Manufacturing Rick Boyd said. “At the same time, we are continuously researching ways to reduce labor stress for our valued team members.”
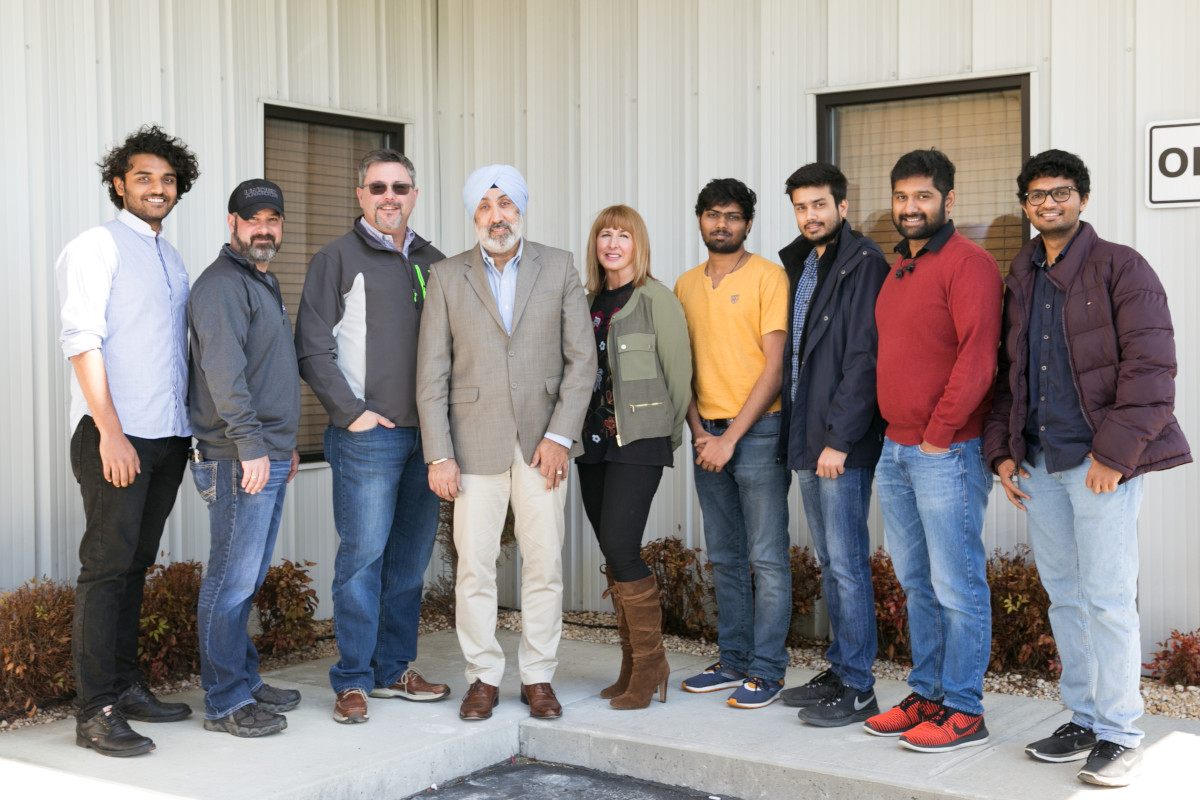
Automation Assists Employees, Benefits Homebuyers
Boyd said automating processes and integrating robotics into the existing production reduces physical burden, but also enhances safety and improves efficiency.
“By testing and incorporating the latest available technology into our construction processes, we hope to deliver innovative and attainable solutions to more home buyers,” he said.
UT engineering faculty and students conducted research during multiple three-week periods at Clayton Rutledge in East Tennessee, one of the company’s 40 off-site home building facilities in the U.S. By using wearable activity trackers and analyzing hours of video, the students compared value-added to non-value-added tasks for each team member throughout the day. They then considered potential time-saving solutions and offered them to the workforce.
“My experience with Clayton had a positive impact on two aspects of my life— problem-solving and relationship management,” UT graduate research assistant Abhay Bajpai said. “Through our research and collaboration, we were able to understand the production process, as well as provide solutions to problems and constraints they were experiencing. The relationships we built with the team members were crucial in our methods for an overall sustainable process improvement.”
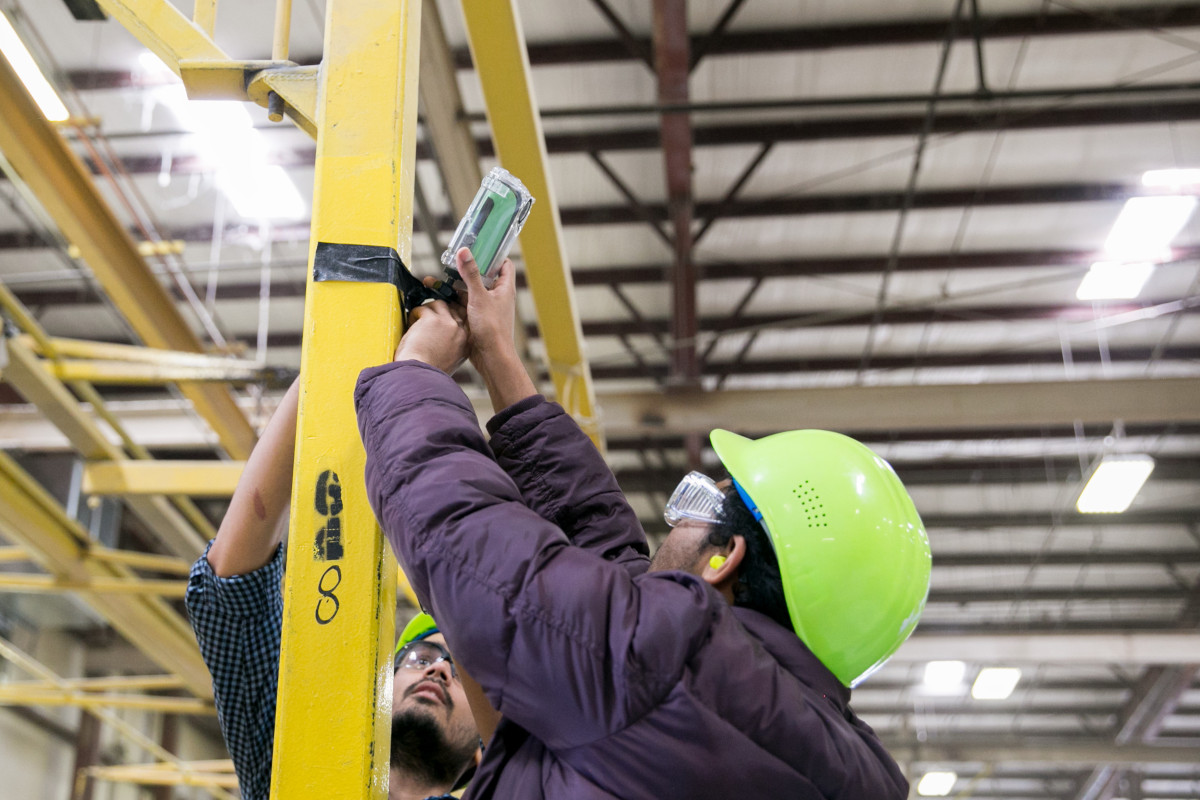
Following the Science of Homebuilding
The National Institute of Building Sciences states that 57% of activities in construction are wasteful and non-value-adding, while 62% add value in manufacturing. As a result of the partnership, changes to improve productivity and team member experience were implemented at several Clayton home building facilities. One of the recommended practices, kitting, involves bundling all materials for a specific space in the home and delivering them at the most accurate time during the building process.
Kitting improves efficiency. Additionally, it encourages physical distancing between team members, which is helpful in reducing the likelihood of virus transmission.
Clayton’s university partnership has delivered meaningful results for manufactured housing, and the research continues, UT Industrial and Systems Engineering Professor at Rupy Sawhney said.
“Not only were we able to create an algorithm and methodology unique to Clayton and the manufacturing industry… that research is now expanding,” Sawhney said. “Several of our staff and students have subsequently developed and published major reports and studies.”
The reason they did this is to help find a better balance for the American workforce between productivity and health and wellness. Sawhney said American workers are very productive, but highly stressed.
Zone-based manufacturing, Sawhney said, is the novel breakthrough his group made during the partnership.
“This basically came from what we saw at Clayton, which was a recommendation toward creating zones within a home where there will be a more strategic work effort on this part of the floor plan. And that’s what led to kitting, where all the materials can be delivered all together and at the right time for a particular zone. We believe through this we can transform productivity and improve the health and wellness of the workforce.”